How Good is Wood?
An excerpt from "The Story of Upfront Carbon" where I am still looking for an answer to that question.
In my last post, a review of Paul Brannen’s Timber!. I expressed some reservations about mass timber, and its role in carbon storage. I wrote about this in my new book, The Story of Upfront Carbon from New Society Publishers. Here is an excerpt from the book where I look at the use of mass timber through the lens of sufficiency. I ask my perennial question, how good is wood? I still do not have an answer, but I thought Paul Brannen made a convincing case that is is very good indeed. Here were my thoughts prior to reading his book.
The North American 2x4 is the core of the most ephemeral of building technologies; our typical home has been described as “an aggregation of toothpicks.” Early settlers might clear their land, square up the wood and build with what we now call timber frame, but as forests got cleared for farmland and lumber was shipped from further away, it became necessary to standardize; by about 1900, lumber was usually two inches thick and boards, one inch. But the saw blades were not thin, and some wood was lost; the wood was also often run through planers and edgers which reduced it further. In 1924 a standard was agreed to that allowed for different tools and technologies, with the so-called 2x4 really being a 1-1/2 by 3-1/2. Vast western spruce and fir and southern pine forests made the standardized 2x4 cheap, and along with inexpensive nails, it made rapid expansion of housing across North America possible.
It is used in everything from starter houses to McMansions; Paul Andersen and Paul Preissner, designers of the US Pavilion at the 2021 Venice Architecture Biennale that was built out of 2x4s told Kate Wagner:[1]
“One of the things that we really like about framing is it’s the same for everybody. It doesn’t matter how rich or poor you are, your house—at least the structure of your house—is all made of the same stuff. No amount of money can buy you a better two-by-four than the one that’s also in the crappiest house in town. I think that’s really democratic, that everybody—you and Beyoncé—has access to the same materials, and they’re the best materials.“
Wood frame construction is not without its problems or limitations. It has to be kept dry, or it becomes food for mold. Wood is not a terrible insulator, but it is not as good as the insulation stuffed around it, so it acts as a thermal bridge. When it is nice and dry, it burns easily. But its flimsiness and flammability have limited its usefulness, which is why building codes prohibited it from being over three stories high until recently. Wood structures could be protected with rated drywall assemblies and sprinklers, but the concrete, masonry, and steel industries lobbied hard to keep wood out of bigger buildings.
With the emergence of the climate crisis, it was quickly recognized that building with wood had a much lower carbon footprint than building with concrete or steel, although how much less is still open to question. But with lightweight wood framing, there was no question at all; there is just so much less weight and less of the stuff. Foundations are smaller, the structure weighs a fraction of concrete. Building codes in many jurisdictions were loosened to allow it in buildings up to 6 storeys high, with sprinklers and full alarm systems; It was cheaper and quicker, too, allowing for greater economies. But it requires good detailing and care while building to control sound transmission and keep the water out. In much of the USA, residential housing is “five over one”- five storeys of wood frame over a concrete ground floor.
In Europe, there never was a culture of building fast and cheap, and light wood frame was never accepted; Europeans are often shocked to find that one can kick or punch their fist through most American walls. Most people lived in apartments with solid clay tile walls, and if they could afford a house, they wanted it to last for generations. Wood might be used for floors and interior walls, but the exteriors were solid load-bearing masonry. The forestry industry was sophisticated and old:[2] “The link between forest production and timber consumption by industrial societies was clearly laid out in 1713 by a Lower Saxony mining administrator called von Carlowitz who gave us the word Nachhaltigkeit or sustainability.” There are no virgin or old-growth forests in Europe; it is all managed.
Given the dislike of light wood framing, there was lots of research into how to use small pieces of wood more efficiently by turning them into bigger pieces of wood.
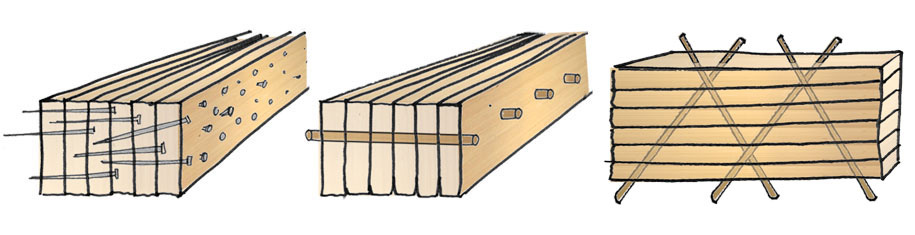
In the 1970s Julius Natterer developed Brettstapel, a method of connecting low-grade timber together without glue. Originally, it was just nailed together, what is now called “Nail Laminated Timber” or NLT. There is nothing new about this; many old warehouses in North America was built with heavy timber columns and beams, with lumber on end nailed together on site. Natterer then developed a version with kiln-dried hardwood dowels hammered into softwood timber; as the dowels absorbed moisture, they would expand, locking the wood together. This is now known as Dowel Laminated Timber (DLT); the largest producer is StructureCraft in Abbotsford, British Columbia.
But the real mass timber revolutions started in Austria in the early 1990s with Gerhard Schickhofer, one of a group of engineers studying laminated wood. Unlike Brettstapel or NLT, where the wood is all parallel, Schickofer laid up his wood crosswise, on top of each other. This could use smaller pieces of wood–our classic 2x4– but was more stable dimensionally and could replace a 2-way slab on columns instead of having to sit on beams. It could use “waste” wood too small for other purposes that could be spliced together. By 1998 the material was approved for construction by the Austrian government, companies like KLH started cranking the stuff out and many small buildings were built out of it.
In 2007, architects Andrew Waugh and Anthony Thistleton convinced a client to let them use CLT in a small apartment building in Hackney, then a not-so-prime part of London. The dubious client agreed but insisted that all the wood be covered with drywall so that none of the tenants would know; he was afraid nobody would want to rent if they did. The result was the first tall urban housing project made entirely of prefabricated CLT panels. The architects write: “Completed within 49 weeks, and delivering 29 fully insulated and soundproof apartments, the project demonstrated for the first time that CLT has the potential to be a financially viable, environmentally sustainable and beautiful replacement for concrete and steel in high-density housing.”
The making of cement and steel is responsible for 15% of global CO2 emissions, so when the green buiding world realized that they could be replaced with mass timber, it took off; every month, there seems to be a new plyscraper claiming to be the tallest wood structure.
Wood is 50% carbon by weight, taken out of CO2 in the atmosphere and combined with hydrogen from water to make cellulose and lignin, respectively, the mass and reinforcing naturally found in wood. The oxygen from the CO2 is released back into the atmosphere.
Many in the industry claim that the wood was carbon-negative (or carbon-positive, depending on who’s talking), storing carbon for the life of the building. It’s true that it is storing carbon, but calling it “carbon-negative” is controversial.
One builder of a Swedish project claimed in a presentation I attended that all the wood in the building was replaced by new growth in Swedish forests in 44 seconds. More recently, the developers of what at the time of writing is the tallest mass timber structure in the world, a glass-clad residential tower in Milwaukee, claim that the wood is ‘replaced’ by natural growth in North American forest in less than 25 minutes. But that means nothing when a forest Is clear cut.
Carbon savings with wood construction are counted in two ways: Avoided emissions, when compared what might have been emitted If building out of concrete or steel. I always thought this was silly, very much like being on a diet and counting the calories of the chocolate cake I didn’t eat, instead of counting only the calories that I do. Others disagree, with Kirksey Architects[3] writing that “Studies accounting for long-term carbon dynamics of wood products shows that the substitution effect of avoiding fossil fuel emissions is even more significant than carbon stored in wood.”
The other carbon saving is from carbon storage in the wood; according to the Mass Timber Institute, [4]“It is estimated that one cubic metre of mass timber sequesters one metric ton of carbon dioxide.” Some have said this is so wonderful, that we should use more wood and store more carbon! But as British engineer Will Hawkins notes[5], “accounting for sequestered carbon is often a source of debate, confusion and inconsistency. When sequestration is reported as a negative emission, it can create the counterintuitive impression that using timber excessively can have environmental benefits.” Hawkins claims carbon uptake in newly planted saplings is initially slow, but then accelerates as these become established. Just harvesting, processing, and constructing a timber building still results in a spike or burp of carbon, whereas sequestration occurs gradually. And “Carbon accounting should always start at zero – credit should not be taken for a tree planted 50 years ago, even if this eventually ends up being used to build the structure under investigation.” The wood doesn’t grow back in minutes or seconds, but will take fifty years until we know that the trees that were cut have been replaced.
Others consider the question of carbon storage in wood construction to be greenwashing, or at best an optimistic stretching of the truth. Alexander Hadley of Failed Architecture[6] fears that demand for mass timber could lead to poor forest practices.
“The seductive simplicity of simply switching from concrete to wood is hard to resist, but it starts to lose its luster as larger scales of interaction come into focus. While most industry advocates admit that the carbon-saving potential for mass timber is predicated on rigorous sustainable forestry management practices, most fail to emphasize the gargantuan effort enacting such practices would take. “
Kirksey architects and others claim that Mass Timber production actually helps the forest.
“Using wood instead of other materials like steel or concrete helps create healthier forests. Using small pieces of lumber for the floors and beams instead of large timber pieces allows manufacturers to leave large trees in the forest. Large trees are better at absorbing carbon from the atmosphere and can help reduce fires and allow the remaining trees to flourish.”
Lever Architects say much the same thing about sustainable forestry.
“It has been shown that forests that are treated as valuable ecosystems—that are managed for multiple benefits in addition to fiber production—have the capacity to improve ecological diversity, foster climate change resilience, reduce catastrophic wildfire risk, while at the same time sustaining the economies of rural communities that have depended on these forests for generations.”
Chris Magwood of Builders for Climate Action wrote a report[7] on emissions from residential construction, and declines to attribute any storage of carbon to timber construction.
“There remain important and unresolved concerns with current accounting methods related to virgin forest products like lumber. Some of these concerns include uncertainty about the amount of carbon released from soils during logging operations; the amount of carbon returning to the atmosphere from roots, slash and mill waste; the amount of carbon storage capacity lost when a growing tree is harvested; and the lag time for newly planted trees to begin absorbing significant amounts of atmospheric carbon dioxide.”
Andy Simmons and journalist Lenny Antonelli write[8] that we should use wood more carefully.
“In Sweden, natural forests are being systematically clear-cut and replaced with even-aged plantations, according to five environmental NGOs. Recent logging of protected forests has also been reported in Estonia, Lithuania, and Romania. And with extractive demand on land increasing, nature is more at risk of being squeezed out. So, while supporting a move from concrete and steel to timber and other natural fibres, our primary goal should be to dramatically reduce the quantity of raw materials needed in the first place. When specifying timber or other natural materials, how efficiently they are used can minimise the pressure on landscapes. As well as prioritising reclaimed or recycled materials where possible, smart choice of build system matters too.”
It is all very confusing; I have been talking about wood construction for well over a decade and have not yet got a definitive answer about how much carbon is stored in mass timber structures and how much is lost along the way. A few years ago, Dave Atkins, an author of the Mass Timber report, told me that “the consensus in the research is that 50 percent of the carbon in the form of wood makes it to the mass timber.” Some wood is left on in the forest specifically to rot and provide animal habitat; some scraps are burned to kiln-dry the wood. But if the trees were left in the forest, fully 100 percent would eventually be released into the air, so 50 percent is pretty good. Atkins also notes that “if you don’t grow it, you mine it.”
Years ago, when I challenged architect Andrew Waugh with the 50% number, his flip answer was “so we’ll plant two trees!” But on a recent visit to his new Black and White building in London, he pointed out how slender the columns and beams were; they were made from Laminated Veneer Lumber (LVL) that is peeled off logs with 90% efficiency. He proudly noted that their buildings now use 40% less fibre than when they started working with mass timber. Much has changed from when architects were proud of how much wood they used.
When I returned from my trip to London, I complained to Peter Moonen of Wood Works Canada that I was no further ahead in understanding the true carbon footprint of mass timber. He said I never would; every forest is different, there are 141 eco-types in Canada alone. Are the roots deep or shallow? What is the temperature or the humidity?
“I think the one thing I can guarantee is that if you do a life-cycle assessment is that it will be wrong.”
All I can do is fall back on the call for sufficiency: How much do we need? Do we really need these silly wood towers, these “plyscrapers?” Or materiality; is it the right stuff for every case? Andrew Waugh, doesn’t think so; he told me that 12-15 storeys are optimum for wood; if you go higher you run into trouble because it is so light. He was much more explicit in a recent quote to Dezeen[9]: “It’s bullshit, because if you’re going to build a tall building in timber, you still have to fill it full of concrete to make sure it doesn’t wave around.” Or efficiency- once wood buildings get tall, the columns get huge and eat up usable space. This is why steel took over from stone in the late 19th century. And finally, there is frugality: is this design achieving more with fewer resources? Is mass timber the best way to build with wood, or can other technologies do more with less?
British architect Piers Taylor has said “Anything below two storeys and housing isn’t dense enough; anything much over five and it becomes too resource intensive.” That’s because mass timber uses four times as much fibre per square foot as does lightweight framing. That’s why the 2X4 is so powerful and important; it lets you use less stuff, our prime directive here.
In Sweden, robots turn 2x4s into multistory houses with quality and precision unheard of in North America. They have redesigned every connection and component for flexibility and repairability. The housing is solid, quiet, comfortable, resilient, and fast.
In the UK, Craig White is building social housing out of prefabricated panels filled with straw. He makes his houses light and moveable so that he can put them on land that might be waiting for development or approvals. He claims it is “less than zero carbon.”
This is not all meant to be a criticism of mass timber! Every square meter of construction where wood replaces steel or concrete can be a plus for the climate, eliminating massive upfront emissions. It is instead a plea to use as little fibre as one can get away with when designing a safe and strong structure.
Perhaps the most pernicious story ever written was The Three Little Pigs, with its very English conclusion that houses should be made of brick. The future we want is built of sticks and straw.
{1} Metropolis https://metropolismag.com/viewpoints/american-framing-venice-biennale/
{2} http://www.fourthdoor.co.uk/unstructured/unstructured_09/extra/brettstapel.php
[3] Kirksey Architects https://www.kirksey.com/about-us/news-media/for-immediate-release/mass-timber-and-sustainability
[4] Mass Timber Institute https://academic.daniels.utoronto.ca/masstimberinstitute/faq/
[5] Will Hawkins, timber and carbon sequestration
{6 Failed Architecture} https://failedarchitecture.com/mass-timber-in-the-age-of-mass-extinction/
{7 Treehugger} https://www.treehugger.com/total-carbon-footprint-north-american-home-report-5225600
{9 Dezeen} https://www.dezeen.com/2023/03/29/building-tall-timber-revolution/
I remember seeing a building under construction in Germany in 2000 in which the floors were solid wood panels, and thinking, why the heck would someone do that when they could use joists? Maximizing the amount of wood in a building is wrong-headed.
A team I've been on is finishing a 3 story, 30,000 sf laboratory building of glulams and CLT. The scale of the spaces means this structural approach replaces steel and concrete. This application makes sense to me.
Note that protection of the wood panels from rain during construction is important, especially if it is going to remain exposed. Using more organic materials subject to mold and decay means upgrading site protection practices. I recently consulted on a project in which straw panels got seriously wet and the straw had to be removed and replaced with another insulation. The manufacturer is considering wrapping future product in plastic membrane to avoid this occurring - this is not an environmental upgrade!
I'm a carpenter and I love working with wood. I'm from Nova Scotia where the forests have been and continue to be raped in the most merciless fashion. We have a zillion miles to go with our forestry practices before we can claim that building with wood is "green". I agree with you, Lloyd. Sufficiency is the number one consideration if we're honestly trying to be green.